Navigation |
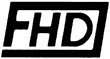
1313
Anvil Rd
Rockford, IL 61115
(815) 282-5161
Fax: (815) 282-5295
|
|
|
 |
PROBLEMS
ENCOUNTERED BY THE CUSTOMER ARISING FROM POOR QUALITY IN THE DIE:
-
Premature
failure, poor extrusion, or hydrolicing of inserts. This
happens with the concave face not allowing the part to fit together
creating undue pressure and friction.
- Heads
of bolts failing. Either
the flange is not flat or the radius in the die is not smooth and tangent.
Even if a radius seems to be print, if it is not symmetrical and tangent,
the end result can be failed parts. Some of these failures are never
identified as the die's quality problem. With out very close inspection,
this problem goes unattended.
- Under
head of bolt not contacting surface completely when screw is used by
customer. This
can be a complex problem for safety parts. If the screw comes back from
heat treater with the bottom of the head not flat, the process of discovering
at what stage of manufacturing process the quality failure happened
is very time consuming. The die face has to be held to a ± 5
minutes for there to be effective control of the finish part.
- Flat
head dies failing prematurely or producing improper angle under the
head. Highly
smooth finishes, flat angles with the correct angle, and tangents radii
are a must if these dies to function to their maximum potential.
Previous
Page | Next Page
|
 |
|