Navigation |
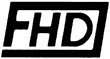
1313
Anvil Rd
Rockford, IL 61115
(815) 282-5161
Fax: (815) 282-5295
|
|
|
 |
The
comparator when used to check depth is only as accurate as the skill
level of the operator. It is critical that the image is focused sharply,
the travels have been calibrated, and the machine is in excellent
condition with digital read out capacities to avoid mixed interpretations.
The power setting must be at least 20x with the ability to go to 50x
if necessary. In the case of shallow angles and intersecting radii,
a theoretically sharp corner has to be determined with overlays for
the reading to be accurate. With some of the more complex readings
a con-trace of the cast is the best choice.
ALTERNATIVE
METHODS OF INSPECTION AND POSSIBLE SHORTCOMMINGS OF THESE PROCESSES:
Gage
pins can and are used for the inspection of I.D. diameters. Pins are
very accurate at determining the round diameter of a hole. They will
not identify any out of roundness, or any back tapers that exist.
On non-round shapes, the pin only identifies the general size and
leaves too much for interpretation to be viewed as highly accurate.
PROBLEMS
ENCOUNTERED BY THE CUSTOMER ARISING FROM POOR QUALITY IN THE DIE:
-
Parts
out of tolerance after heading. If
the die isn't thoroughly correct, all aspects of the heading
process suffer. Any incorrect dimensions not discovered in the
header die will have to be corrected, if possible, by later
operations at the screw manufacturer's time and expense.
-
Incorrect
press fits of inserts assembled in cases. Many
die failures are caused by incorrect press fit. Both too much and
too little. This is caused by tri-round O.D.s, inaccurate measurement
of the parts, and inexperienced Die Makers assuming incorrectly the
proper press needed.
-
Parts
not fitting correctly in subsequent dies in multi-die set ups. It
is imperative to make sure that the engineering done in multi-station
formers is not undermined by die components that are not exactly to
specifications denoted by the engineer.
|
 |
|